
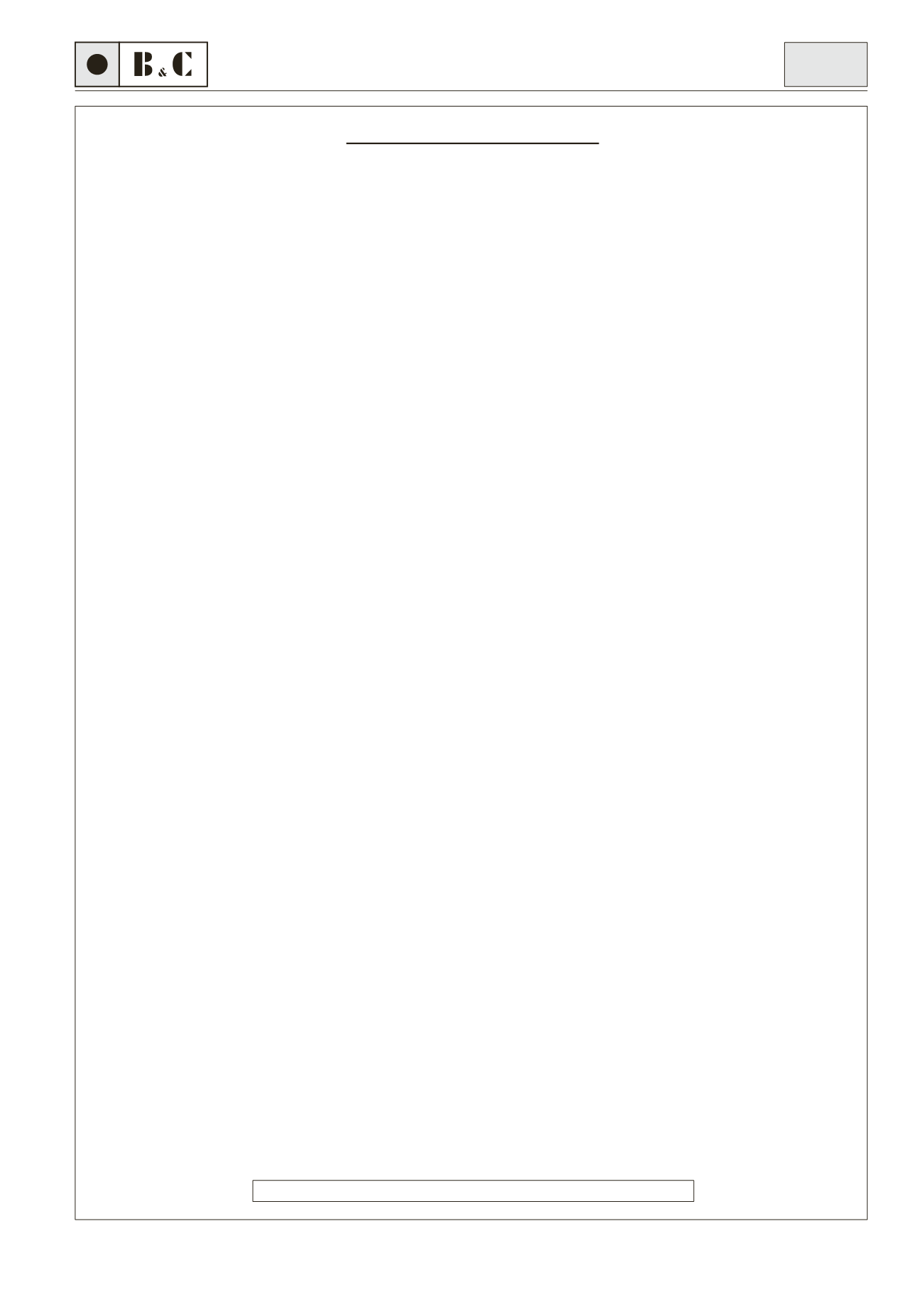
35
HQ
© 2008 B
&
C
Maximum speed:
the maximum speeds given in this catalogue are valid for an atmospheric pressure of 1 bar (14.7
psi) and with ambient temperature in the range of +30
°
C to +50
°
C. Higher speeds than those given cause a reduction
in the volumetric efficiency, due to cavitation phenomena in the inlet area inside the pump. Sustained excess speed
causes a rapid deterioration of the internal components reducing the lifetime of the cartridge.
Minimum speed:
In general, the min. speed for all pumps is 600 rpm. However, it is possible to operate at lower
speeds with certain pump configurations and with appropriate operating temperatures.
Inlet pressure:
the inlet pressure, measured at the inlet port, should remain within the prescribed limits. Note that
pressures lower than minimum limit cause cavitation and pressures above the maximum limit cause abnormal loads
on the shaft and the bearings. In both cases this causes a significant reduction in the lifetime of the cartridge.
Maximum outlet pressure:
the maximum outlet pressure is different for each type of fluid used as can be seen from
the corresponding diagrams. With optimal temperature and filtration conditions a pressure peak of +10% is permissible
for a maximum time of 0.5 sec.
Mounting and drive connections:
consider the following indications when preparing the installation drawings for the
system:
• avoid axial and radial loads on the shaft;
• the mounting flange has to be perpendicular to the drive shaft, with a maximum error of 0.18 mm every 100 mm;
• when mounting onto a gearbox, or other component without a flexible coupling, it is advisable to check the clearance
between splines that has to be between 0.013 and 0.051 mm on the pitch diameter.
Hydraulic circuit:
always install a pressure relief valve on the supply line to prevent the pressure from exceeding
the allowed maximum. Normally, it is set in accordance with the weakest component in the system. (In the case where
it is the pump, set the valve to a pressure 15% higher than the maximum pressure rating of the pump.)
Inlet line tubing should have a section equal to or greater than that of the inlet port of the pump. It is advisable to keep
the tube connecting the pump to the reservoir as short possible. Particular care has to be taken with the inlet line
which has to be hermetically sealed to avoid entraining air into the circuit; this varies the characteristics of the hydraulic
fluid causing the operating parts to become damaged.
Filtration:
the inlet line filter must have a flow rate capacity that is higher than that of the pump at its maximum
operating speed. The filtration requirements for individual models are given in this catalogue. The use of a filter by-
pass is recommended for cold starts and should the filter become clogged. Proper maintenance of the filter element
is essential for the correct operation of the entire system. In normal conditions replace the filter element after the first
50 hours of operation. Subsequently, replace it at least every 500 hours. Regarding the filter on the return line, the
same general conditions apply as for the inlet line and it should be positioned in an accessible location for ease of
maintenance.
Tank:
if possible, the reservoir should be positioned above the pump. Otherwise, ensure that the minimum level of
the fluid contained in it is higher than the pump inlet line opening. It is important to avoid draining the inlet line with
the pump at standstill. The opening of the return line into the reservoir must remain below the minimum level of the
fluid in the reservoir. It must not be positioned too close to the opening of the inlet line to avoid the possibility of any
air bubbles passing into the inlet line. Baffles inside the reservoir may be useful in avoiding the problem. Rapid
temperature changes can cause condensation on the underside of the lid of the reservoir with the formation of droplets
of water that can fall into the oil. To avoid this problem it is recommended that the lid should have small vents so that
the air space in the reservoir is ventilated. The vents have to be screened, though, to prevent the entry of dust or the
sudden expulsion of fluid.
Start-up:
use the following procedure when the pump is started-up for the first time:
completely fill the pump and the inlet line with fluid;
start the engine for approximately one second a number of times at regular intervals of approximately 2 or 3 seconds
until the noise level reduces, thereby confirming that it has been primed;
with a manometer check to ensure that the outlet pressure increases slightly;
once the pump has been primed, maintain low pressure levels activating all parts of the circuit a number of times until
air bubbles disappear completely from the return line to the reservoir.
This procedure should be carefully as any residual air inside the pump can quickly cause the rotor to seize.
Cold starting:
when starting the pump, especially with low ambient temperatures, operate with moderate speed and
pressure until the average temperature in the entire circuit is within the given limits.
The information provided in this catalogue is subject to change without notice
Operating instructions